Globally, there is an increasing trend towards prefabrication and modular construction as landowners, developers, building companies and engineers look for sound ways to improve the commercial viability of projects.
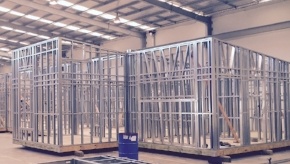

Modular Construction offers a truly revolutionary way to redefine the building process with countless applications (bathroom pods, school classrooms, hotel rooms, bedroom apartments, office buildings, relief housing, military installations). Modules are assembled into any size or shape desired and can be fitted next to one another or stacked. They are pre-wired for electricity and fitted for plumbing, heating, and internal finishes before leaving the factory floor.
With offsite construction, individual modules of the building are transported to the construction site, set into place by cranes and assembled onsite, which offers a stable, secure building structure on a reduced timeframe.
The FRAMECAD System is the perfect solution to enable light gauge steel (LGS) prefab and modular construction. In this article, we list 5 scenarios where LGS (also known as cold-formed steel (CFS)) prefabricated and steel framing in modular construction methods are advantageous to builders, project owners and developers alike.
How many of the scenarios (below) can you benefit from in your construction projects?
5 scenarios or situations where LGS/CFS modular construction is a superior building method…
1. Geographic locations where traditional methods are not optimum
Construction in areas with high wind speeds and/or seismic activity, salt-spray zones and other challenging environmental locations will often make traditional methods of construction difficult, uneconomic or unsustainable.
The innate characteristics of LGS – such as its reliability to resist rusting, warping, bending or breaking – mean LGS construction is ideally suited to these locations and can open up more development opportunities.
2. Sites with confined or restricted access
In the past, the construction of buildings in difficult access areas or in situations where there is no access to infrastructure, such as disaster zones, has been notoriously difficult to undertake. But now with LGS prefabrication and modular construction, frames and building sections, and pods can be constructed and assembled off-site and easily transported to site, reducing overall construction lead times and costs.
3. Construction in regional/remote locations
Construction in regional or remote locations often means weak infrastructure, lack of natural resources and little labor available onsite meaning higher building cost and potential delays will occur. However, LGS modular construction overcome the challenges named above, as pods are transported directly to site and require minimal skilled labor devoted to on-site erection.
4. Complex projects where a high degree of quality and control is needed
Modular solutions in a factory environment exercise a greater degree of planning and control over construction quality compared to on-site workmanship. The efficiency and accuracy of LGS and the FRAMECAD System, using modular construction means that construction projects adhere to strict quality guidelines, meaning each and every project are produced to spec.
5. Modular Construction Timelines - Projects with strict timelines
CFS modular construction is faster than traditional methods at every step in the design, specification, manufacture and construction phases of a construction project. Operating in a factory-controlled environment means each prefabricated building part or pod is manufactured respecting strict timelines. The construction phase onsite also becomes easier, reducing erection time. CFS Modular construction offers a lower level of risk and a much more predictable schedule than traditional methods of construction.
For further reading visit Myths about Modular Construction, Permanent vs Non-permanent and Prefabrication and Modular Construction.