Introduction
Are you working with cold formed steel (CFS) or considering FRAMECAD technology for your next construction project? From choosing the right stud sizes to understanding span limits and profile systems, builders often face critical questions that affect time, cost and performance.
In this article, I answer ten of the most frequently asked questions about FRAMECAD systems and cold-formed steel, also known as light gauge steel construction, giving you practical insights to avoid costly mistakes and maximize efficiency on-site.
Getting Started with Cold Formed Steel: The 10 Most Common Technical Questions Answered
The difference between 3-1/2” and 3-5/8” (or 5-1/2” and 6”) studs mainly comes down to convention, not technical requirements. In general, residential construction uses 3-1/2” and 5-1/2” studs, while commercial projects tend to favor 3-5/8” and 6”. There is no scientific or technical reason for that at all. It is just industry practice. The key thing to watch is compatibility: most doors, windows, and hardware are sized for residential dimensions, so mismatched framing can lead to costly problems. The same caution applies in commercial contexts - always match framing sizes with the fixtures specified for that sector.
The span of a FRAMECAD webbed joist or truss isn’t fixed - it’s determined by a combination of factors including load requirements, spacing between members, steel thickness, joist or truss depth and the grade of steel used. By adjusting any of these parameters, it’s possible to meet a wide range of span requirements to suit the structural design. Essentially, the system offers flexibility to match the specific needs of each project.
Yes, FRAMECAD systems are well-suited for constructing mid-rise buildings ranging from four to eight stories. The most commonly used profiles for this type of construction include 6" (12 or 14-gauge – 97 or 68 mil) and 3-5/8" (20-gauge – 33 mil). These profiles allow for the efficient design and construction of multi-story structures. Early project planning is critical - involving the architect and all relevant trades from the outset helps reduce the risk of design changes, rework, or on-site reinforcements. In some areas of the building, hot-rolled steel may still be required, but cold-formed steel is typically used where it offers both structural and cost advantages.
While multi-profile systems offer flexibility by producing a wider range of profiles, they also come with added complexity, requiring more operator experience, longer changeover times, and a larger variety of coil stock. Dedicated profile systems, by contrast, are built for speed and simplicity. They streamline production, reduce training requirements, minimize downtime, and lower inventory needs. Many companies find that running multiple dedicated systems can actually deliver higher total output than relying on a single multi-profile machine.
Webbed joists and deep C joists are both suitable for residential and commercial applications, but they differ significantly in production and installation. Webbed joists can be manufactured using any FRAMECAD system and offer excellent flexibility for installing services like plumbing and electrical. However, they tend to require more labor during fabrication. Deep C joists, by comparison, are quicker to produce but need a heavy platform system and are typically limited to just one or two depth options. Installing services through C joists often requires large openings, which adds to system weight and complexity. For longer spans, webbed joists can be adapted by increasing their depth or modifying other design factors.
ICC certification (or a recognised equivalent) is essential because building codes require product manufacturers to have quality systems in place that ensure compliance with minimum code standards. This certification involves an independent third-party auditor verifying that the steel profiles produced by FRAMECAD systems meet regulatory requirements. The process includes full traceability - tracking each profile from raw material through to installation - to confirm that high-quality steel and consistent manufacturing practices are used throughout construction.
To find an engineer for your cold-formed steel (CFS) building, FRAMECAD maintains a global network of certified engineering consultants familiar with both the FRAMECAD system and its software. These professionals are trained to design for efficient manufacturing and structural performance using CFS. Additionally, the Cold-Formed Steel Engineers Institute (CFSEI) offers a directory of experienced engineers in the CFS field - although not all of them may work directly with FRAMECAD technology, they can still be valuable design partners depending on your project.
Sourcing steel coils takes some industry knowledge. Most fabricators purchase coils through steel service centers, though larger operations may work directly with mills or major roll formers. Some also look to offshore suppliers. Regardless of the source, it's crucial to verify that the coils meet international standards like ASTM, particularly in terms of thickness, strength, galvanized coating, and exact coil width. ICC certification helps confirm these criteria are met. A useful rule to remember is: you buy steel by weight but sell it by length, so coil thickness should match design specs as closely as possible to avoid costly oversupply or underperformance.
FRAMECAD is the most widely adopted end-to-end steel framing system globally, built specifically to meet the demands of manufacturers, general contractors, developers, and builders frustrated by delays, rising material costs, and insufficient support. It empowers users with full control over production and materials, offering both dedicated and multi-profile systems to suit businesses of any scale. Unlike other providers, FRAMECAD delivers an integrated solution - combining advanced roll-forming machinery with in-house engineering, detailing software, and a full range of accessories. With global 24/7 support and expert-led training across all aspects of the system, FRAMECAD offers both speed and reliability backed by extensive industry certification.
When building single-family homes with cold-formed steel, typically only one or two profile sizes are required - most commonly the 3-1/2” and 5-1/2” profiles. The 5-1/2” profile is generally used for exterior walls, especially in areas with higher structural demands like wind, snow, or seismic loads. Interior walls, floor joists, and roof trusses are often built using the 3-1/2” profile. Contrary to a common misconception, larger profiles are not needed in steel framing to accommodate more insulation - that’s more relevant to timber construction. In many cases, the 3-1/2” profile is sufficient for an entire home, particularly in regions with low to moderate loading requirements. Joist and stud spacing at 24” on center is typically the most efficient approach, though 16” spacing can be used if the design demands it. FRAMECAD’s F325iT and F450iT systems are well-suited for producing all necessary framing components for single-family homes.
Conclusion
Whether you're building single-family homes or multi-story structures, understanding the details of FRAMECAD systems and steel framing is essential for efficient, code-compliant construction. With the right profiles, planning and support, you can streamline production and avoid costly errors - no matter the project scale.
Want to learn more about how cold-formed steel framing can transform your next project? Reach out to our industry experts.
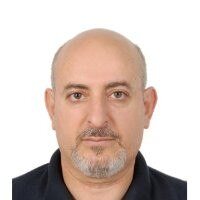