Multi-family Community Pivots Construction from Wood to Steel Realizes Lower Costs and Accelerated Project Delivery by 30%
Traditional wood construction methods often fail to deliver the speed, design flexibility, and quality that modern projects demand. As owners and developers push for resilient structures delivered on time and within budget, cold-formed steel (CFS) framing is gaining popularity.
CFS manufacturers like Intellisteel are seizing the opportunity and delivering projects with speed, quality and efficiency that keep owners and developers coming back for more. Based in Groveland, Florida, Intellisteel designs, engineers and manufactures CFS structures. The company uses FRAMECAD’s end-to-end solution to design, manufacture, build and deliver CFS components.
Intellisteel’s founder and CEO, Stanley Adwell, sees CFS as a solution to the construction industry's inefficiencies, cost overruns, and lack of skilled labor. “We can deliver high-quality CFS structures in half the time it would take with traditional methods, all while cutting costs and reducing the need for onsite labor,” he said. “You just can’t match the speed of CFS construction.”
Adwell also points to rising insurance premiums as another reason behind the growing demand for CFS. “Steel is non-combustible and lowers the risk of fire-related incidents, which are a primary concern for insurance providers. It is also resilient to flooding and seismic events. Developers can benefit from substantially lower insurance premiums by opting for steel framing.”
The high insurance cost led DTN Management to consider CFS for a 300,000 sq. ft. luxury multi-family community in Michigan. The project, Vista at Brighton, was permitted for wood framing and well underway, but DTN Management gave Intellisteel an opportunity to prove that they could do the work for less.
“Our bid to build with CFS reduced the cost by $5 per square foot before factoring in the savings from lower insurance premiums,” said Adwell. “After seeing that CFS framing would reduce premiums and deliver a high quality, resilient structure with a lower total cost of ownership, DTN Management invested in converting the project to CFS.”
Collaboration, Alignment and Speed
Intellisteel began working with the project’s general contractor, Wolverine Group. One of the top general contractors in the country, Wolverine Group has 80 years of experience in design-build, construction management and general contracting. The project’s superintendent, John Law, recalls learning about the decision to use CFS for the frames and trusses. “The project manager asked what I thought, and I was all for it,” he said. “I was a metal stud framer before becoming a superintendent, so I was on board from the moment they said steel.”
Intellisteel incorporates Design for Manufacturing and Assembly (DfMA) principles into every project. With DfMA, all stakeholders are brought to the table early to collaborate, align and communicate, ensuring that every decision enhances efficiency, from manufacturing to assembly. “From day one, Intellisteel worked closely with our team and other project stakeholders, including MEP contractors, to convert the framing and trusses from wood to CFS,” said Law.
Using FRAMECAD software, Intellisteel detailed the machine-ready components in 3D, generating production-ready files that a FRAMECAD roll-forming machine would use to transform rolls of coiled steel into each component with precision. The FRAMECAD machine manufactured the CFS components to exact specifications with MEP holes pre-drilled and labeled. Intellisteel then shipped the components to the jobsite for fast and error-free assembly.
“Intellisteel converted the drawings from wood to steel extremely quickly,” said Law. “They brought in the MEP contractors to incorporate their parts into the FRAMECAD system. With 233 apartments, roughly 58 per floor, each unit has at least 2-3 plumbing stacks that could get in the way of studs and trusses. Intellisteel took the time to ensure everything would fit together seamlessly on-site.”
From start to finish, the project moved at a pace that caught the attention of other contractors and developers. “The quality and speed are pretty incredible,” said Law. “Early on, I flew down to see how the work was progressing. Intellisteel had been producing for a relatively short period and had already finished the first floor, just shy of 40 semi-trucks of material. Developers and contractors reached out asking to tour the jobsite. The speed of construction garnered attention, but the cleanliness of the jobsite also drew eyes to the project. We didn’t have as much waste. A jobsite looks more organized when you have nice, clean piles of material coming off the trucks and going right into the work zones.”
Intellisteel delivered the CFS trusses and frames cut to the exact length, with service and fastener holes pre-punched, studs pre-swaged and pre-notched for quick and easy assembly, requiring less labor on site. “Installing the CFS framing is significantly faster because it is a lot more precise and requires fewer modifications in the field,” said Law. “The precision and the speed at which they can put it together on the jobsite is fantastic.”
Steel is also straight and has less variance than other materials. “We don't have to account for nearly as much creep when putting together large hallways,” said Law. “I have a 300-foot-long hallway on this project, and I could look down that hallway before the drywall went on and see how straight it was because there was no warping. There was no differential settlement. When putting shear walls together, we can tighten them down immediately and keep going. CFS gives us a much more rigid building during the construction process. At peak efficiency, we installed 20,000 square feet of load-bearing walls and trusses weekly.”
Wolverine Group completed the project on time. “Had the project started the way we finished with Intellisteel, we would have finished the framing in just four months, which would have been two months ahead of schedule, or 30 percent faster than traditional methods,” said Law.
![]() |
![]() |
Growing Demand for CFS
There is a common misconception that CFS is more expensive than wood. “We compete directly with and beat wood pricing on hard costs alone before the other cost to build benefits,” said Adwell. “We can design and engineer and have come in at a lower cost than wood on every single project we have across 21 states.”
CFS also delivers a lower total cost of ownership. “The accelerated delivery that comes with CFS reduces the interest owners carry and accelerates time to occupancy, which equates to dollars,” he said. “The precision of CFS eliminates rework and waste. The durability of CFS and resistance to mold, pests and warping mean lower costs to maintain the building. Also, insurance rates drop dramatically when you go from wood to steel. It is evident from the increase in demand that more and more owners and developers are recognizing that building with CFS costs less than wood and delivers long-term value.”
While the adoption of CFS is growing, some people are slow to embrace change. “Most people think, if it's not broken, don't fix it,” said Law. “Change is hard, but in our experience, transitioning to CFS was easy and seamless. From my perspective, CFS is significantly faster and ergonomically efficient because it is lighter and easier to move around. It's more precise and predictable, which makes our work easier overall. To me, it's a no-brainer. In my opinion, CFS delivered with Intellisteel and FRAMECAD is just a better way to build.”
Want to learn more about how cold-formed steel framing can transform your next project? Reach out to industry experts and explore our case studies to see the advantages in action.
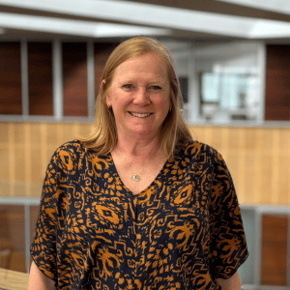