Introduction - Optimizing the Supply Chain with Steel Framing
The US residential construction industry has witnessed its fair share of challenges in recent years, with supply chain disruptions, fluctuating material prices, and environmental concerns taking center stage.
In this article, we explore a solution that can help developers and builders take control of their supply chain by utilizing steel framing. We delve into the ways cold-formed steel framing can provide stability, sustainability and control in the ever-evolving landscape of US residential construction.
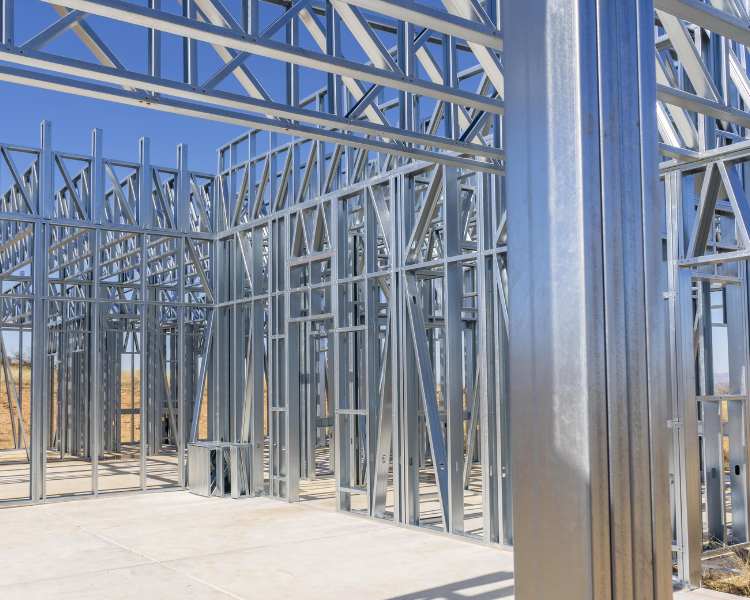
The Current Supply Chain Challenges
Before we get into the specifics of steel framing, let's take a closer look at the supply chain issues that have been plaguing US residential construction:
Lumber Price Volatility
The industry has grappled with unpredictable lumber prices, leading to budget overruns and delayed projects due to soaring costs.
Environmental Concerns
As environmental awareness grows, using traditional wood framing has raised concerns about deforestation and carbon emissions, pushing builders to seek more sustainable alternatives.
Supply Chain Disruptions
Natural disasters have highlighted vulnerabilities in the supply chain, resulting in production delays, transportation challenges, and material shortages.
The Steel Framing Solution
By incorporating cold-formed steel (CFS) into construction projects, the value chain can be enhanced, offering a steady supply, accelerated timelines and design flexibility. These advantages contribute to a streamlined, efficient and cost-effective construction process that benefits all stakeholders involved.
Unlike wood, which is subject to variations and availability steel coils don’t warp, ensuring consistent uniformity and accessibility. The regulated and standardized product of steel enables better supply chain planning and control over material availability, minimizing delays and ensuring that construction projects stay on schedule.
Steel framing stands as a robust solution that can help control supply chain challenges in the US residential construction industry. Here's how:
Supply Chain Stability
CFS framing components are manufactured in controlled environments, reducing the impact of external factors like weather and transportation disruptions. This stability translates to more predictable timelines and costs.
Sustainability
Cold-formed steel is an inherently sustainable material. It's 100% recyclable, reduces the need for deforestation, and minimizes carbon emissions. Embracing steel can align your construction projects with eco-conscious consumers' demands.
Cost Control
Steel prices tend to be more stable compared to lumber prices, making it easier for developers to estimate project costs accurately. This control mitigates the risk of budget overruns and financial surprises.
![]() |
![]() |
Logistics
Steel's lightweight nature and high strength-to-weight ratio means it can be contained, stored, and transported in a compact coil. This makes it easier to handle and store, requiring significantly less storage footprint compared to wood. The lighter weight also facilitates more efficient transportation, reducing shipping costs and coordination complexities. Additionally, steel does not require special treatment for moisture, pests, or decay during transit, simplifying the logistics process. With its stable, engineered properties and consistent attributes, CFS ensures a high standard of finish.
Waste Reduction
There is less waste during construction when using cold-formed steel. Precise manufacturing means fewer onsite cuts, leading to reduced material waste and disposal costs.
Enhanced Durability
The superior strength of steel and its durability results in homes that can withstand extreme conditions and have a longer lifespan. This reduces the need for frequent repairs and renovations, offering long-term cost savings.
Faster Construction
Prefabricated steel framing components are easier to install, significantly speeding up the construction process. This efficiency minimizes project delays, ensuring developments reach the market sooner.
Summary
As developers and builders navigate the complex landscape of US residential construction, the adoption of CFS framing emerges as a powerful tool to take control of the supply chain. Its stability, sustainability, cost predictability, waste reduction and durability can reshape the industry's future, offering long-term benefits for both builders and homeowners.
By integrating cold formed steel framing into US residential construction projects, not only are developers addressing the challenges that have plagued the supply chain, but they are also actively contributing to the development of a more sustainable and resilient construction industry. It's time to take control of the supply chain and build a better future with steel framing.
You may also be interested in reading, fire safety with steel framing, savings with steel framing, steel framing boosts resilience and smart cities with steel framing.
Discover more in our residential eBook.
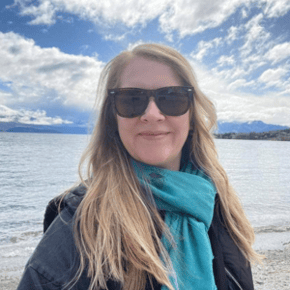